Moulding properties of ikole ekiti silica–clay mixture for foundry application
Keywords:
Foundry, Pattern-making, Casting, Moulding Sand, Silica, and Ikole Sand.Abstract
This study focuses on the characterisation of Ikole Ekiti sand for foundry application, and the mould properties of the sand such as Clay Content, Shatter Index, Permeability, and Green Strength. Dry Strength and Refractoriness were investigated. The characterization of Ikole Natural Sand and Synthetic Moulding Sand (Ikole Natural Sand and River Sand bonded with clay respectively) were examined in order to determine their suitability for Foundry Mould production. The sand samples were taken from three sites, rinsed, and dried in the sun for three days to remove any water. The sand samples were sieved via a British Standard (BS) sieve to get the desired grain size for the experiment. Powdered moulding sand was then thoroughly mixed by hand for about 10 minutes with clean water to create a homogeneous sand-water combination. Each sample was then moulded in a specimen tube using a standard sand rammer to create standard test specimens measuring 50 mm by 50 mm. With the addition of a binder to the Ikole Natural Sand some of the physical properties were improved. From the results, an addition of 5% Clay, results in the following change in values; Shatter Index (from 3% to 20%), Permeability (from 65 to 60), Green Strength (from 75.15 to 95.14kN/m2 for compression, and 14.48 to 17.23kN/m2 for shear) and Dry Strength (399.89 to 482.63kN/m2 for compression and 103.42 to 127.55kN/m2 for shear). The synthetic moulding sand has improved foundry moulding properties for foundry application than the other sands in this study.
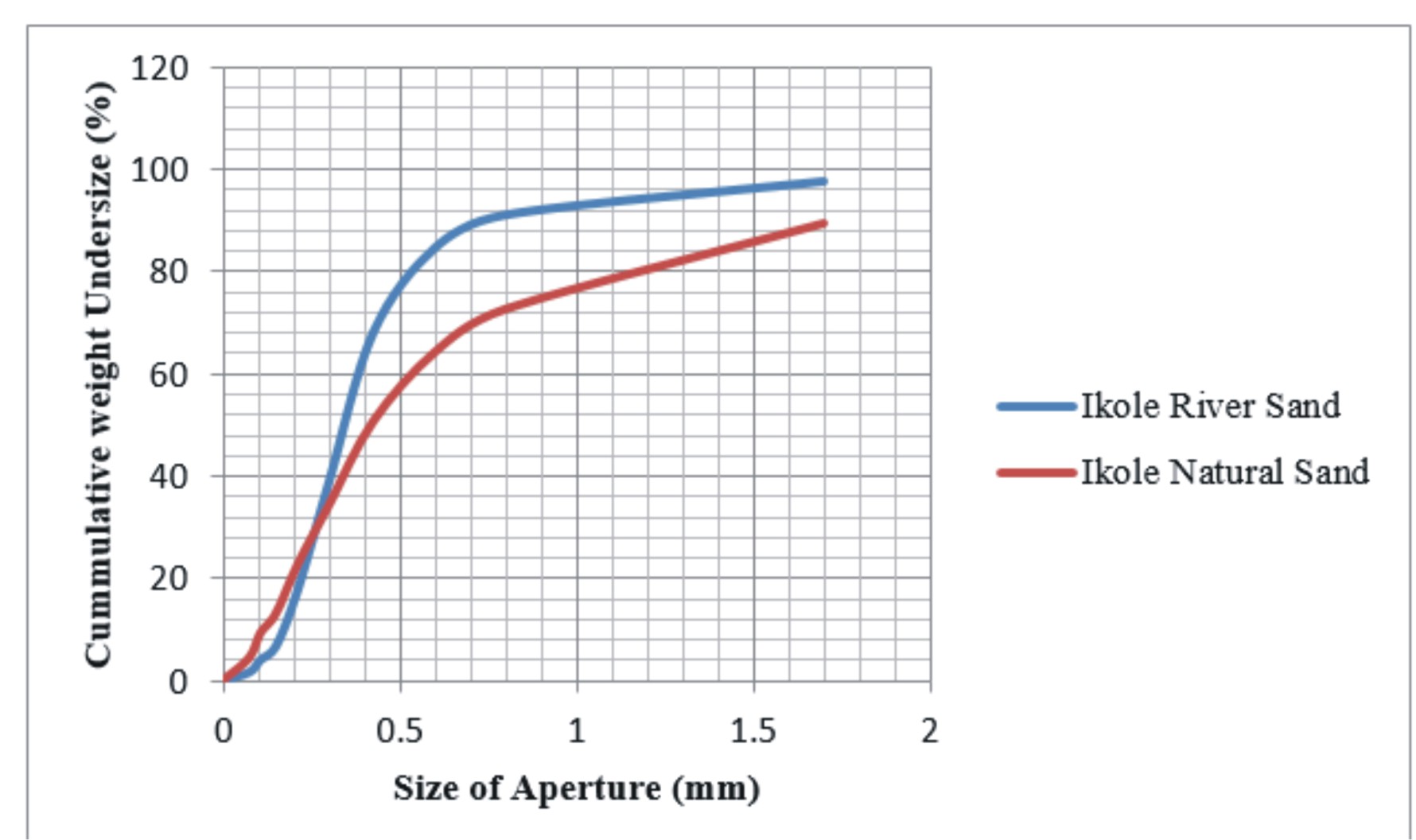